Discovering the Advancements and Applications of Laser Technology
Laser-cutting technology is the slitting process used to cut metallic and non-metallic substances of varying thicknesses. In this process, a controlled coherent beam of light is focused on the objects intended to be cut. The focused laser beam results in the material melting, burning, or vaporizing in a particular pattern. Laser cutting is a noncontact process, where the material is cut without contact, thus making it suitable to cut fragile and brittle substances.
How does it work?
The laser beam is generated by a focused and directed high-intensity light by the laser cutting machine. The beam of light is sourced from the laser cavity. The laser rod present inside the laser cavity generates radiation. The light has small bundles of the photon, and the atom of the rod are stimulated by these photons. Further the stimulated atoms generate multiple photons having the same wavelength, phase, and direction. Again, the new photons produced energize the atom to produce a cascade of energized photons, and the resulting photons become the laser beam.
There are three main types of laser-cutting technology used in laser-cutting machines. The types differ in the material used to generate laser beams. Below discussed is the type of lasers-
The CO2 cutting laser:
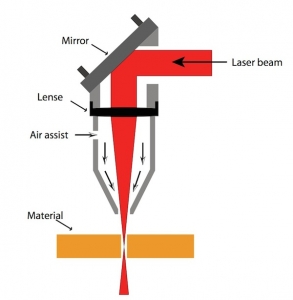
This is among the most common types of laser-cutting technology used for cutting non-metallic materials like wood, plastics, and acrylics. A laser beam is generated by the laser machine in the presence of a gaseous mixture of carbon dioxide, nitrogen, and helium to generate the laser beam.
Fiber-optic Laser
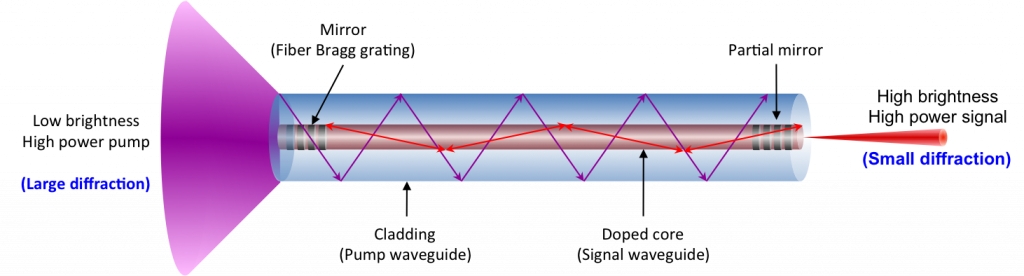
Fiber-optic lasers are the most advanced type of laser cutting. The light beam of different wavelengths is generated for more precise cutting. The optic fiber used is made of silica glass that guides the beam of light. The laser beam produced is small and straight which aids precise cutting.
The laser source mixture comprises ytterbium-doped, thulium-doped, and erbium-doped. This composition of the mixture depends upon the application, as the wavelength of the beam depends on the composition used.
Nd-YAG (Neodymium Yttrium-Aluminium-Garnet) lasers
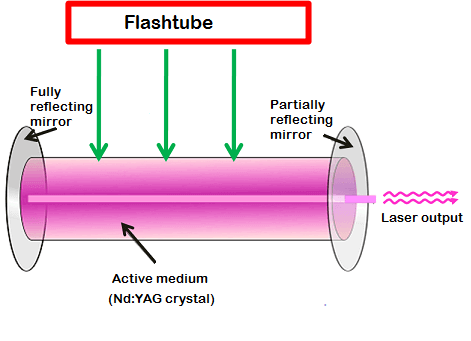
This is a solid-state laser that uses a synthetic crystal as a laser medium.
This type is used to cut materials like ceramics and metals. The solid-state laser medium is made of Neodymium Yttrium-Aluminium-Garnet. Krypton flashlamps and laser diodes are used to achieve laser pumping. Laser pumping excites the Nd molecules, the excited Nd molecules become stable without emitting photons. The metastable state of Nd molecules releases infrared light to form a laser beam.
Each laser cutting type has its strength and weakness, and the choice of laser cutting type depends upon its application.
Why use Laser tech, how does it benefit the user?
Laser-cutting machines are widely used in manufacturing, electronics, and aerospace. Below are some benefits of using laser cutting technology–
Non-contact technique:
The laser cutting technique involves no conventional cutting tools, hence saving the material or tool from wear or damage. On the other side, conventional cutting is slow and produces heat, thus the chances of distorting the material are high.
Precision and Accuracy:
Laser beams are focused on the target, this allows precise cutting. This process is highly automated and digitally controlled. Repeated and consistent results are achieved by setting the required parameters.
Suitable for crystal and brittle materials:
The laser can cut crystals, ceramics, or brittle materials. Besides this laser can also cut the high strength materials like titanium and steel alloys
High aspect ratio:
The lasers can drill holes of very small diameter. Whereas drilling holes by conventional methods can cause noise, and heat, and can have chances of breakage.
Fast speed:
Since there is no requirement to manually position the material, the speed of cutting solely depends on the configuration and power of the cutting head. The time can be further reduced by investing high in the laser machine price.
No Residual Waste:
The most molten residual is cleared by gas medium, no residual stress is left, and clean and sharp edges are obtained.
Minimum burrs:
Since manufacturing demands and more precise finished product. laser cutting technology used in manufacturing offers deburring effect to obtain superior edge quality products.
No-contact cutting:
The Laser cutting technology is a non-contact process, which means that there is no actual contact between the laser and the material under process which ultimately reduces the damage risk to the material, making it an essential tool when cutting delicate fabrics is involved.
Conclusion
The laser cutting technology available today is one of the best developments happening with its several advantages of high precision, speed, and others, making it a very appealing option to put to use.